Reliability Engineer
Arima or Arouca or Piarco, North East
Full time
Posted On 11.22.2024
Expire On 12.23.2024 Employer
Description
Department: Reliability & Projects
Division: Operations
Reports To: Reliability Superintendent
Division Head: Director - Operations
POSITION SUMMARY
The Reliability Engineer identifies and manages asset reliability risks that could adversely affect plant or business operations. The incumbent utilizes engineering principles to support manufacturing and production processes to ensure the Converting and Mill plant machines and equipment are more efficient and dependable.
RESPONSIBILITES
- Create comprehensive listings of critical spare parts to align with all Failure Modes and Effects Analysis (FMEA) tasks
- Develop and maintain a document library of Standard Maintenance Procedures (SMPs) to support any critical and complex tasks from Preventative Maintenance (PM) activities
- Provide technical Support during outages and at breakdowns to gain valuable technical experience
- Support the Projects Department in developing scope of works, creating detail Gantt charts, perform basic modifications in CAD software, organising various project dossiers.
- Provide support to the Team’s reliability goals, both short and long term.
- Support the Maintenance Team daily, including but not limited to, assisting with troubleshooting for major breakdowns and advising on short-term and medium-term actions to enhance machine reliability.
- Assist in analysing failure modes for Mechanical and E&I equipment and components.
- Collaborate with the Maintenance Planners in preparing work orders, requisitions & procedures; prioritize jobs based on reliability data, A3, Asset Critical Levels (ACLs) and work order listing.
- Participate in the planning of upcoming shutdowns.
- Support the achievement of the department’s KPIs - completion of A3s, breakdown rate, Mean Time To Repair (MTTR), Mean Time Between Failures (MTBF)
- Attend related departmental meetings
- Provide support and ensure all safety systems, power systems and Distributed Control Systems (DCS) are well maintained and operational.
- Inform the Superintendent on outstanding issues and pending risks.
- Actively participate in activities to build team spirit at every level of the organization.
- Support in the documentation process regarding breakdowns, projects and upgrades.
- Adhere to, actively promote and ensure compliance with the Company’s Health and Safety Policies.
- Report any unsafe acts immediately to your Direct Supervisor; operate in a safe manner, using Personal Protective Equipment (PPE) when required.
- Execute all relevant responsibilities as outlined in the Roles, Responsibilities and Authorities Matrix (MT-GM-004) to ensure compliance with the Integrated Management System (IMS).Perform any other related duties that may be assigned.
EDUCATION & TRAINING
- A Bachelor’s Degree in Mechanical or Electrical Engineering or any other related discipline from a recognized institution.
EXPERIENCE
- A minimum of two (2) years’ experience in a similar role in a manufacturing environment.
- Experience in troubleshooting, control circuits, Proportional Integral Derivative (PID) loops, pneumatics systems, Programmable Logic Controls (PLC) and making recommendations.
SKILLS & COMPETENCIES
- Proficient in Microsoft Office Suite
- Ability to read mechanical, electrical and hydraulic drawings and manuals
- Strong written / verbal communication
- Strong presentation skills
- Ability to build and maintain positive, constructive relationships, networking
- Report writing
- Strong analytical skills
- Self-motivated
- Proactive
- Attention to detail / accuracy
- Prioritization & deadline oriented
- Professional
- Innovative
- Ability to lead and influence
- Critical thinking
- Independent decision making
- Troubleshooting
- Solution oriented / problem solving
- Strong planning & organization
- Time management
- Confidential
- Initiative
- Ability to multi-task and work in a fast-paced environment
- Continuous Improvement
- Change Management
CONTACTS
- All team members
- External Contractors
- Suppliers
WORKING CONDITIONS AND ENVIRONMENT
- Exposure to dust, noise, heat
- Possible low indoor air quality
- Occasional heavy lifting
- Standing/walking for long periods
- Repetitive motion
- Plant environment
- Regular use of computers
- Operating equipment
- Working extended hours when required
PERSON PROFILE
- Operates with honesty and integrity, demonstrating high ethical and professional standards
- Generates trust and credibility in interactions with fellow team members, customers, suppliers, government agencies and the community
- Is respectful and fosters sincere collaboration
- Makes appropriate and reliable decisions
- Is determined in the face of challenges
- Has a passion for excellence
- Customer Service oriented
- Is innovative, challenges the status quo and aims to add value to the Company’s operations
- A team player
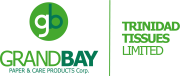
Trinidad Tissues Limited
View Company Profile
View Saved Jobs Tell a Friend Print This Ad Report This Job
Overview
Tags
Installation-Maintenance-Repair : Facilities Management-Maintenance, General-Other: Installation-Maintenance-Repair
Job Requirements
- A Bachelor’s Degree in Mechanical or Electrical Engineering or any other related discipline from a recognized institution.
EXPERIENCE
- A minimum of two (2) years’ experience in a similar role in a manufacturing environment.
- Experience in troubleshooting, control circuits, Proportional Integral Derivative (PID) loops, pneumatics systems, Programmable Logic Controls (PLC) and making recommendations.
Career Advice
BROWSE JOBSThe Right Time to Seek Feedback After a Job Application or Interview
Maximize Your Chances by Following Up at the Right Time Job hunting can be a challenging process and receiving little to no feedback on submitted applications can be frustrating According to a poll…
Read More